What are the Product Standards for Resistor Classification?
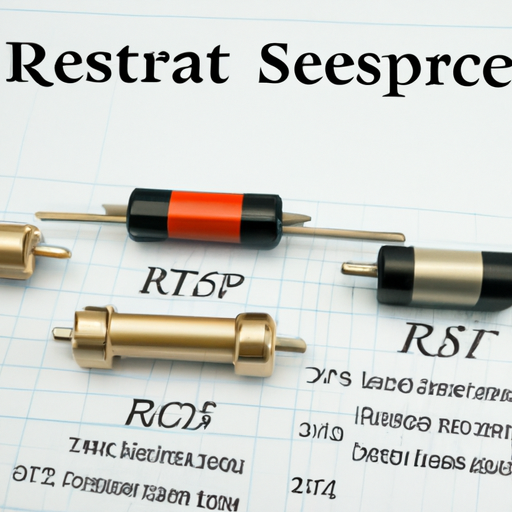
I. Introduction
Resistors are fundamental components in electronic circuits, serving the essential function of limiting current flow and dividing voltages. They come in various types and specifications, making resistor classification crucial for engineers and manufacturers. Understanding the product standards that govern resistor classification ensures that these components meet the necessary performance, reliability, and safety requirements. This blog post will explore the different types of resistors, key product standards, classification criteria, testing methods, applications, challenges, and future trends in resistor standards.
II. Understanding Resistor Types
A. Fixed Resistors
Fixed resistors are the most common type, providing a constant resistance value. They can be categorized into several subtypes:
1. **Carbon Composition Resistors**: Made from a mixture of carbon and a binding material, these resistors are known for their high energy absorption and ability to withstand high temperatures. However, they have a higher tolerance and lower stability compared to other types.
2. **Metal Film Resistors**: These resistors are made by depositing a thin layer of metal onto a ceramic substrate. They offer better stability, lower noise, and tighter tolerances than carbon composition resistors, making them suitable for precision applications.
3. **Wirewound Resistors**: Constructed by winding a metal wire around a ceramic or fiberglass core, wirewound resistors can handle high power levels and are often used in power applications. They are known for their accuracy and stability but can be bulkier than other types.
B. Variable Resistors
Variable resistors allow for adjustable resistance values, making them versatile in various applications.
1. **Potentiometers**: These are commonly used for adjusting voltage levels in circuits, such as volume controls in audio equipment. They consist of a resistive element and a movable contact.
2. **Rheostats**: Similar to potentiometers but designed to handle higher currents, rheostats are used to control current flow in applications like lighting and motor speed control.
C. Specialty Resistors
Specialty resistors serve specific functions beyond standard resistance.
1. **Thermistors**: These temperature-sensitive resistors change resistance with temperature variations, making them ideal for temperature sensing and compensation applications.
2. **Photoresistors**: Also known as light-dependent resistors (LDRs), these components change resistance based on light exposure, commonly used in light-sensing applications.
III. Key Product Standards for Resistors
Product standards play a vital role in ensuring the quality and reliability of resistors. Several organizations establish these standards:
A. International Electrotechnical Commission (IEC) Standards
1. **IEC 60115**: This standard outlines general specifications for fixed resistors, including performance characteristics, testing methods, and reliability requirements.
2. **IEC 60393**: This standard focuses on resistors used in electronic equipment, providing guidelines for their performance and safety.
B. American National Standards Institute (ANSI) Standards
1. **ANSI/IEEE C57.12.00**: This standard specifies requirements for resistors used in power applications, ensuring they can handle the electrical and thermal stresses encountered in such environments.
C. Joint Electron Device Engineering Council (JEDEC) Standards
1. **JESD22**: This standard addresses reliability testing for resistors, ensuring that they can withstand various environmental conditions and stresses over time.
D. Other Relevant Standards
1. **RoHS Compliance**: The Restriction of Hazardous Substances (RoHS) directive limits the use of specific hazardous materials in electronic components, including resistors.
2. **REACH Regulations**: The Registration, Evaluation, Authorisation, and Restriction of Chemicals (REACH) regulations ensure that chemical substances used in resistors are safe for human health and the environment.
IV. Classification Criteria for Resistors
Resistor classification is based on several criteria that determine their suitability for specific applications:
A. Resistance Value
The resistance value, measured in ohms, is a primary classification criterion. Resistors are available in a wide range of ohmic values, with tolerances indicating the allowable deviation from the specified resistance.
B. Power Rating
Power rating, measured in watts, indicates the maximum power a resistor can dissipate without overheating. Proper thermal management is crucial to prevent failure, especially in high-power applications.
C. Temperature Coefficient
The temperature coefficient measures how much a resistor's resistance changes with temperature. A low temperature coefficient is desirable for precision applications, as it indicates better stability across varying temperatures.
D. Voltage Rating
The voltage rating specifies the maximum operating voltage a resistor can handle. Exceeding this rating can lead to breakdown and failure, making it essential to consider in circuit design.
E. Tolerance Levels
Tolerance levels indicate the precision of a resistor's resistance value. Common tolerances include ±1%, ±5%, and ±10%, with tighter tolerances preferred for high-precision applications.
V. Testing and Quality Assurance
Ensuring the quality and reliability of resistors involves rigorous testing and quality assurance processes.
A. Testing Methods for Resistors
1. **Resistance Measurement Techniques**: Various methods, such as the four-wire measurement technique, are used to accurately measure resistance, minimizing the impact of lead resistance.
2. **Power Rating Tests**: Resistors undergo power rating tests to verify their ability to handle specified power levels without overheating or failing.
B. Quality Assurance Processes
1. **Manufacturing Standards**: Adhering to established manufacturing standards ensures that resistors are produced consistently and meet performance specifications.
2. **Inspection and Testing Protocols**: Regular inspection and testing throughout the manufacturing process help identify defects and ensure compliance with product standards.
VI. Applications of Resistor Standards
Resistor standards are critical across various industries, ensuring that components perform reliably in diverse applications:
A. Consumer Electronics
In consumer electronics, resistors are used in devices like televisions, smartphones, and audio equipment, where performance and reliability are paramount.
B. Industrial Equipment
Industrial applications often require resistors that can withstand harsh conditions, making adherence to standards essential for safety and performance.
C. Automotive Applications
In automotive electronics, resistors play a crucial role in systems like engine control units and safety features, where reliability is critical.
D. Medical Devices
Medical devices require high precision and reliability, making compliance with resistor standards vital for patient safety and device performance.
VII. Challenges in Resistor Classification
Despite the established standards, several challenges persist in resistor classification:
A. Evolving Technology and Standards
As technology advances, new materials and manufacturing techniques emerge, necessitating updates to existing standards to ensure they remain relevant.
B. Globalization and Standardization Issues
With the globalization of the electronics market, differing standards across regions can create challenges for manufacturers and engineers seeking to ensure compliance.
C. Counterfeit Components
The proliferation of counterfeit components poses a significant risk to the integrity of electronic systems. Ensuring that resistors meet established standards is crucial for preventing failures due to substandard components.
VIII. Future Trends in Resistor Standards
The landscape of resistor standards is evolving, influenced by several trends:
A. Innovations in Resistor Technology
Advancements in materials and manufacturing processes are leading to the development of new resistor types with improved performance characteristics.
B. Impact of IoT and Smart Devices
The rise of the Internet of Things (IoT) and smart devices is driving demand for resistors with enhanced functionality and reliability, necessitating updates to existing standards.
C. Sustainability and Environmental Considerations
As environmental concerns grow, there is an increasing emphasis on sustainability in electronics manufacturing, prompting the development of standards that address environmental impact.
IX. Conclusion
In conclusion, resistor classification and adherence to product standards are vital for ensuring the reliability and performance of electronic components. Understanding the various types of resistors, key standards, classification criteria, and testing methods is essential for manufacturers and engineers alike. As technology continues to evolve, staying informed about the latest trends and challenges in resistor standards will be crucial for maintaining high-quality electronic systems. Manufacturers and engineers are encouraged to prioritize compliance with established standards to ensure the safety and effectiveness of their products.
X. References
1. International Electrotechnical Commission (IEC) Standards
2. American National Standards Institute (ANSI) Standards
3. Joint Electron Device Engineering Council (JEDEC) Standards
4. RoHS Compliance Guidelines
5. REACH Regulations Documentation
This comprehensive overview of product standards for resistor classification highlights the importance of these components in electronic systems and the need for adherence to established standards to ensure quality and reliability.
What are the Product Standards for Resistor Classification?
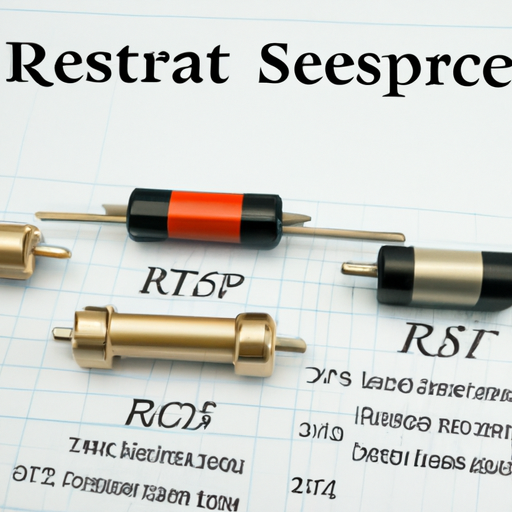
I. Introduction
Resistors are fundamental components in electronic circuits, serving the essential function of limiting current flow and dividing voltages. They come in various types and specifications, making resistor classification crucial for engineers and manufacturers. Understanding the product standards that govern resistor classification ensures that these components meet the necessary performance, reliability, and safety requirements. This blog post will explore the different types of resistors, key product standards, classification criteria, testing methods, applications, challenges, and future trends in resistor standards.
II. Understanding Resistor Types
A. Fixed Resistors
Fixed resistors are the most common type, providing a constant resistance value. They can be categorized into several subtypes:
1. **Carbon Composition Resistors**: Made from a mixture of carbon and a binding material, these resistors are known for their high energy absorption and ability to withstand high temperatures. However, they have a higher tolerance and lower stability compared to other types.
2. **Metal Film Resistors**: These resistors are made by depositing a thin layer of metal onto a ceramic substrate. They offer better stability, lower noise, and tighter tolerances than carbon composition resistors, making them suitable for precision applications.
3. **Wirewound Resistors**: Constructed by winding a metal wire around a ceramic or fiberglass core, wirewound resistors can handle high power levels and are often used in power applications. They are known for their accuracy and stability but can be bulkier than other types.
B. Variable Resistors
Variable resistors allow for adjustable resistance values, making them versatile in various applications.
1. **Potentiometers**: These are commonly used for adjusting voltage levels in circuits, such as volume controls in audio equipment. They consist of a resistive element and a movable contact.
2. **Rheostats**: Similar to potentiometers but designed to handle higher currents, rheostats are used to control current flow in applications like lighting and motor speed control.
C. Specialty Resistors
Specialty resistors serve specific functions beyond standard resistance.
1. **Thermistors**: These temperature-sensitive resistors change resistance with temperature variations, making them ideal for temperature sensing and compensation applications.
2. **Photoresistors**: Also known as light-dependent resistors (LDRs), these components change resistance based on light exposure, commonly used in light-sensing applications.
III. Key Product Standards for Resistors
Product standards play a vital role in ensuring the quality and reliability of resistors. Several organizations establish these standards:
A. International Electrotechnical Commission (IEC) Standards
1. **IEC 60115**: This standard outlines general specifications for fixed resistors, including performance characteristics, testing methods, and reliability requirements.
2. **IEC 60393**: This standard focuses on resistors used in electronic equipment, providing guidelines for their performance and safety.
B. American National Standards Institute (ANSI) Standards
1. **ANSI/IEEE C57.12.00**: This standard specifies requirements for resistors used in power applications, ensuring they can handle the electrical and thermal stresses encountered in such environments.
C. Joint Electron Device Engineering Council (JEDEC) Standards
1. **JESD22**: This standard addresses reliability testing for resistors, ensuring that they can withstand various environmental conditions and stresses over time.
D. Other Relevant Standards
1. **RoHS Compliance**: The Restriction of Hazardous Substances (RoHS) directive limits the use of specific hazardous materials in electronic components, including resistors.
2. **REACH Regulations**: The Registration, Evaluation, Authorisation, and Restriction of Chemicals (REACH) regulations ensure that chemical substances used in resistors are safe for human health and the environment.
IV. Classification Criteria for Resistors
Resistor classification is based on several criteria that determine their suitability for specific applications:
A. Resistance Value
The resistance value, measured in ohms, is a primary classification criterion. Resistors are available in a wide range of ohmic values, with tolerances indicating the allowable deviation from the specified resistance.
B. Power Rating
Power rating, measured in watts, indicates the maximum power a resistor can dissipate without overheating. Proper thermal management is crucial to prevent failure, especially in high-power applications.
C. Temperature Coefficient
The temperature coefficient measures how much a resistor's resistance changes with temperature. A low temperature coefficient is desirable for precision applications, as it indicates better stability across varying temperatures.
D. Voltage Rating
The voltage rating specifies the maximum operating voltage a resistor can handle. Exceeding this rating can lead to breakdown and failure, making it essential to consider in circuit design.
E. Tolerance Levels
Tolerance levels indicate the precision of a resistor's resistance value. Common tolerances include ±1%, ±5%, and ±10%, with tighter tolerances preferred for high-precision applications.
V. Testing and Quality Assurance
Ensuring the quality and reliability of resistors involves rigorous testing and quality assurance processes.
A. Testing Methods for Resistors
1. **Resistance Measurement Techniques**: Various methods, such as the four-wire measurement technique, are used to accurately measure resistance, minimizing the impact of lead resistance.
2. **Power Rating Tests**: Resistors undergo power rating tests to verify their ability to handle specified power levels without overheating or failing.
B. Quality Assurance Processes
1. **Manufacturing Standards**: Adhering to established manufacturing standards ensures that resistors are produced consistently and meet performance specifications.
2. **Inspection and Testing Protocols**: Regular inspection and testing throughout the manufacturing process help identify defects and ensure compliance with product standards.
VI. Applications of Resistor Standards
Resistor standards are critical across various industries, ensuring that components perform reliably in diverse applications:
A. Consumer Electronics
In consumer electronics, resistors are used in devices like televisions, smartphones, and audio equipment, where performance and reliability are paramount.
B. Industrial Equipment
Industrial applications often require resistors that can withstand harsh conditions, making adherence to standards essential for safety and performance.
C. Automotive Applications
In automotive electronics, resistors play a crucial role in systems like engine control units and safety features, where reliability is critical.
D. Medical Devices
Medical devices require high precision and reliability, making compliance with resistor standards vital for patient safety and device performance.
VII. Challenges in Resistor Classification
Despite the established standards, several challenges persist in resistor classification:
A. Evolving Technology and Standards
As technology advances, new materials and manufacturing techniques emerge, necessitating updates to existing standards to ensure they remain relevant.
B. Globalization and Standardization Issues
With the globalization of the electronics market, differing standards across regions can create challenges for manufacturers and engineers seeking to ensure compliance.
C. Counterfeit Components
The proliferation of counterfeit components poses a significant risk to the integrity of electronic systems. Ensuring that resistors meet established standards is crucial for preventing failures due to substandard components.
VIII. Future Trends in Resistor Standards
The landscape of resistor standards is evolving, influenced by several trends:
A. Innovations in Resistor Technology
Advancements in materials and manufacturing processes are leading to the development of new resistor types with improved performance characteristics.
B. Impact of IoT and Smart Devices
The rise of the Internet of Things (IoT) and smart devices is driving demand for resistors with enhanced functionality and reliability, necessitating updates to existing standards.
C. Sustainability and Environmental Considerations
As environmental concerns grow, there is an increasing emphasis on sustainability in electronics manufacturing, prompting the development of standards that address environmental impact.
IX. Conclusion
In conclusion, resistor classification and adherence to product standards are vital for ensuring the reliability and performance of electronic components. Understanding the various types of resistors, key standards, classification criteria, and testing methods is essential for manufacturers and engineers alike. As technology continues to evolve, staying informed about the latest trends and challenges in resistor standards will be crucial for maintaining high-quality electronic systems. Manufacturers and engineers are encouraged to prioritize compliance with established standards to ensure the safety and effectiveness of their products.
X. References
1. International Electrotechnical Commission (IEC) Standards
2. American National Standards Institute (ANSI) Standards
3. Joint Electron Device Engineering Council (JEDEC) Standards
4. RoHS Compliance Guidelines
5. REACH Regulations Documentation
This comprehensive overview of product standards for resistor classification highlights the importance of these components in electronic systems and the need for adherence to established standards to ensure quality and reliability.