Common Production Processes for High-Voltage Parallel Capacitors
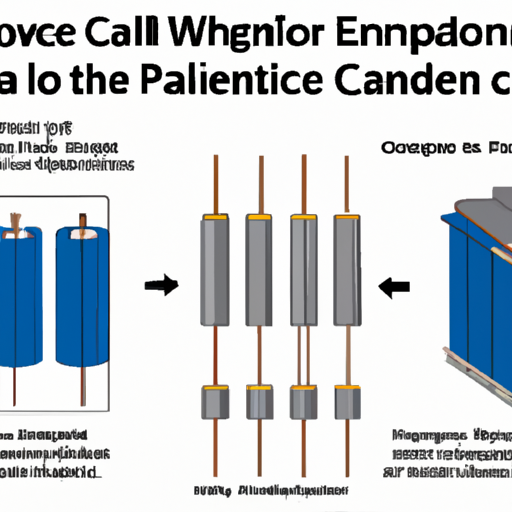
I. Introduction
High-voltage parallel capacitors are essential components in various electrical systems, playing a critical role in energy storage, power factor correction, and voltage regulation. These capacitors are designed to operate at high voltage levels, making them indispensable in applications such as power transmission, renewable energy systems, and electric vehicles. Understanding the production processes involved in creating high-voltage parallel capacitors is crucial for manufacturers and engineers alike, as it ensures the reliability and efficiency of these components in demanding environments.
II. Materials Used in High-Voltage Parallel Capacitors
A. Dielectric Materials
The dielectric material is a key component of high-voltage capacitors, as it separates the conductive plates and stores electrical energy. Common types of dielectrics include ceramic, film, and electrolytic materials. Each type has unique properties that make it suitable for specific applications. For instance, ceramic dielectrics are known for their high dielectric strength and stability, while film dielectrics offer excellent thermal and electrical performance. The choice of dielectric material is critical, as it must withstand high voltages without breaking down, ensuring the capacitor's longevity and reliability.
B. Conductive Materials
Conductive materials, such as aluminum and copper, are used for the electrodes in high-voltage capacitors. These materials must possess high conductivity to minimize energy losses and ensure efficient operation. Additionally, they should have good thermal properties to withstand the heat generated during operation. The selection of conductive materials is vital, as it directly impacts the capacitor's performance and efficiency.
C. Insulating Materials
Insulation is crucial in high-voltage applications, as it prevents electrical leakage and ensures safety. Common insulating materials include epoxy resins, silicone, and various polymers. These materials must exhibit excellent dielectric properties, mechanical strength, and resistance to environmental factors such as moisture and temperature fluctuations. The choice of insulation material is essential for maintaining the integrity and safety of high-voltage capacitors.
III. Design Considerations
A. Electrical Specifications
When designing high-voltage parallel capacitors, several electrical specifications must be considered. The voltage rating is a critical parameter, as it determines the maximum voltage the capacitor can handle without failure. Additionally, the capacitance value, which indicates the capacitor's ability to store charge, must be carefully selected based on the application requirements. Tolerance levels are also important, as they define the acceptable range of capacitance values during operation.
B. Physical Dimensions
The physical dimensions of high-voltage capacitors are influenced by various factors, including size constraints and form factor considerations. Manufacturers must balance the need for compact designs with the requirements for heat dissipation and mechanical stability. The form factor can also impact the capacitor's integration into electrical systems, making it essential to consider these aspects during the design phase.
C. Environmental Factors
High-voltage capacitors must operate reliably in various environmental conditions. Factors such as temperature and humidity resistance are critical, as extreme conditions can lead to capacitor failure. Additionally, capacitors must be designed to withstand mechanical stress and vibration, especially in applications such as electric vehicles and industrial machinery. Addressing these environmental factors during the design process is essential for ensuring the long-term performance of high-voltage capacitors.
IV. Production Processes
A. Material Preparation
The production of high-voltage parallel capacitors begins with material preparation. This involves sourcing high-quality raw materials and conducting thorough quality control checks to ensure they meet the required specifications. Pre-treatment processes for dielectrics and conductors may also be necessary to enhance their performance characteristics. For example, dielectric materials may undergo surface treatments to improve adhesion during layer formation.
B. Dielectric Layer Formation
The dielectric layer is a critical component of high-voltage capacitors, and its formation involves several techniques. Coating methods, such as spraying and dipping, are commonly used to apply dielectric materials to the conductive plates. Film extrusion and lamination are also popular methods for creating dielectric layers, particularly in film capacitors. Once the dielectric layer is applied, curing and drying processes are essential to ensure proper adhesion and performance.
C. Electrode Fabrication
Electrode fabrication is another crucial step in the production of high-voltage capacitors. Various methods can be employed to produce electrodes, including foil stamping and screen printing. These techniques allow for precise control over the electrode dimensions and properties. After fabrication, electrode assembly techniques are used to align and stack the electrodes with the dielectric layers, ensuring optimal performance.
D. Capacitor Assembly
The assembly of high-voltage capacitors involves careful stacking and alignment of the dielectric and electrode layers. This process is critical for ensuring uniformity and consistency in the final product. Once assembled, the capacitors undergo encapsulation and sealing processes to protect them from environmental factors and mechanical stress. Proper encapsulation is essential for maintaining the integrity and reliability of high-voltage capacitors.
E. Testing and Quality Assurance
Testing and quality assurance are vital components of the production process for high-voltage capacitors. Electrical testing, including voltage breakdown and capacitance measurement, ensures that the capacitors meet the required specifications. Mechanical testing, such as vibration and thermal cycling tests, assesses the capacitors' durability under real-world conditions. Compliance with industry standards, such as IEC and UL, is also crucial for ensuring the safety and reliability of high-voltage capacitors.
V. Challenges in Production
A. Material Limitations
One of the significant challenges in the production of high-voltage capacitors is the availability of high-quality materials. Sourcing materials that meet the stringent requirements for high-voltage applications can be difficult and costly. Additionally, the performance of high-voltage capacitors is often dependent on the quality of the materials used, making it essential for manufacturers to invest in reliable suppliers.
B. Process Optimization
Balancing production speed and quality is another challenge faced by manufacturers. While increasing production rates can lead to cost savings, it may also compromise the quality of the final product. Manufacturers must continuously seek ways to optimize their processes, reduce waste, and improve efficiency without sacrificing quality.
C. Technological Advancements
The integration of automation and robotics in the production process presents both opportunities and challenges. While these technologies can enhance efficiency and precision, they also require significant investment and expertise. Additionally, staying abreast of innovations in materials and design is essential for manufacturers to remain competitive in the market.
VI. Future Trends in High-Voltage Capacitor Production
A. Emerging Materials and Technologies
The future of high-voltage capacitor production is likely to be shaped by emerging materials and technologies. Nanomaterials, for example, hold great potential for enhancing the performance of capacitors, offering improved dielectric properties and energy density. Advances in dielectric materials, such as high-k dielectrics, may also lead to more compact and efficient capacitor designs.
B. Sustainability in Production
Sustainability is becoming increasingly important in the production of high-voltage capacitors. Manufacturers are exploring eco-friendly materials and processes to reduce their environmental impact. Recycling and waste management practices are also gaining attention, as companies seek to minimize waste and promote a circular economy in capacitor production.
C. Market Demand and Applications
The demand for high-voltage capacitors is expected to grow in response to the increasing adoption of renewable energy systems and electric vehicles. As these technologies continue to evolve, the need for reliable and efficient capacitors will become even more critical. Manufacturers must be prepared to adapt to changing market demands and explore new applications for high-voltage capacitors.
VII. Conclusion
High-voltage parallel capacitors play a vital role in modern electrical systems, and understanding their production processes is essential for ensuring their reliability and efficiency. From material selection to assembly and testing, each step in the production process contributes to the overall performance of these components. While challenges such as material limitations and process optimization persist, advancements in technology and a focus on sustainability are shaping the future of high-voltage capacitor manufacturing. As the demand for these components continues to grow, manufacturers must remain agile and innovative to meet the evolving needs of the industry.
Common Production Processes for High-Voltage Parallel Capacitors
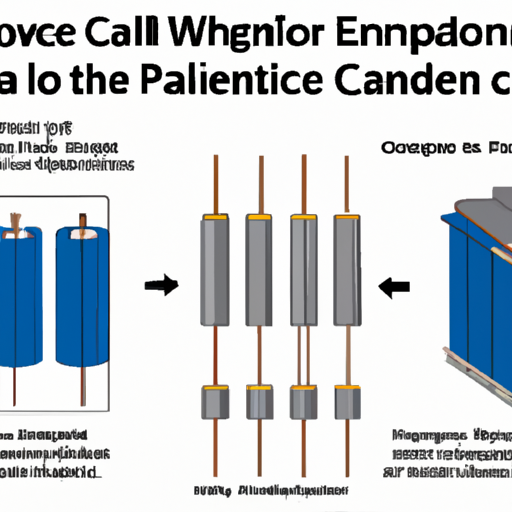
I. Introduction
High-voltage parallel capacitors are essential components in various electrical systems, playing a critical role in energy storage, power factor correction, and voltage regulation. These capacitors are designed to operate at high voltage levels, making them indispensable in applications such as power transmission, renewable energy systems, and electric vehicles. Understanding the production processes involved in creating high-voltage parallel capacitors is crucial for manufacturers and engineers alike, as it ensures the reliability and efficiency of these components in demanding environments.
II. Materials Used in High-Voltage Parallel Capacitors
A. Dielectric Materials
The dielectric material is a key component of high-voltage capacitors, as it separates the conductive plates and stores electrical energy. Common types of dielectrics include ceramic, film, and electrolytic materials. Each type has unique properties that make it suitable for specific applications. For instance, ceramic dielectrics are known for their high dielectric strength and stability, while film dielectrics offer excellent thermal and electrical performance. The choice of dielectric material is critical, as it must withstand high voltages without breaking down, ensuring the capacitor's longevity and reliability.
B. Conductive Materials
Conductive materials, such as aluminum and copper, are used for the electrodes in high-voltage capacitors. These materials must possess high conductivity to minimize energy losses and ensure efficient operation. Additionally, they should have good thermal properties to withstand the heat generated during operation. The selection of conductive materials is vital, as it directly impacts the capacitor's performance and efficiency.
C. Insulating Materials
Insulation is crucial in high-voltage applications, as it prevents electrical leakage and ensures safety. Common insulating materials include epoxy resins, silicone, and various polymers. These materials must exhibit excellent dielectric properties, mechanical strength, and resistance to environmental factors such as moisture and temperature fluctuations. The choice of insulation material is essential for maintaining the integrity and safety of high-voltage capacitors.
III. Design Considerations
A. Electrical Specifications
When designing high-voltage parallel capacitors, several electrical specifications must be considered. The voltage rating is a critical parameter, as it determines the maximum voltage the capacitor can handle without failure. Additionally, the capacitance value, which indicates the capacitor's ability to store charge, must be carefully selected based on the application requirements. Tolerance levels are also important, as they define the acceptable range of capacitance values during operation.
B. Physical Dimensions
The physical dimensions of high-voltage capacitors are influenced by various factors, including size constraints and form factor considerations. Manufacturers must balance the need for compact designs with the requirements for heat dissipation and mechanical stability. The form factor can also impact the capacitor's integration into electrical systems, making it essential to consider these aspects during the design phase.
C. Environmental Factors
High-voltage capacitors must operate reliably in various environmental conditions. Factors such as temperature and humidity resistance are critical, as extreme conditions can lead to capacitor failure. Additionally, capacitors must be designed to withstand mechanical stress and vibration, especially in applications such as electric vehicles and industrial machinery. Addressing these environmental factors during the design process is essential for ensuring the long-term performance of high-voltage capacitors.
IV. Production Processes
A. Material Preparation
The production of high-voltage parallel capacitors begins with material preparation. This involves sourcing high-quality raw materials and conducting thorough quality control checks to ensure they meet the required specifications. Pre-treatment processes for dielectrics and conductors may also be necessary to enhance their performance characteristics. For example, dielectric materials may undergo surface treatments to improve adhesion during layer formation.
B. Dielectric Layer Formation
The dielectric layer is a critical component of high-voltage capacitors, and its formation involves several techniques. Coating methods, such as spraying and dipping, are commonly used to apply dielectric materials to the conductive plates. Film extrusion and lamination are also popular methods for creating dielectric layers, particularly in film capacitors. Once the dielectric layer is applied, curing and drying processes are essential to ensure proper adhesion and performance.
C. Electrode Fabrication
Electrode fabrication is another crucial step in the production of high-voltage capacitors. Various methods can be employed to produce electrodes, including foil stamping and screen printing. These techniques allow for precise control over the electrode dimensions and properties. After fabrication, electrode assembly techniques are used to align and stack the electrodes with the dielectric layers, ensuring optimal performance.
D. Capacitor Assembly
The assembly of high-voltage capacitors involves careful stacking and alignment of the dielectric and electrode layers. This process is critical for ensuring uniformity and consistency in the final product. Once assembled, the capacitors undergo encapsulation and sealing processes to protect them from environmental factors and mechanical stress. Proper encapsulation is essential for maintaining the integrity and reliability of high-voltage capacitors.
E. Testing and Quality Assurance
Testing and quality assurance are vital components of the production process for high-voltage capacitors. Electrical testing, including voltage breakdown and capacitance measurement, ensures that the capacitors meet the required specifications. Mechanical testing, such as vibration and thermal cycling tests, assesses the capacitors' durability under real-world conditions. Compliance with industry standards, such as IEC and UL, is also crucial for ensuring the safety and reliability of high-voltage capacitors.
V. Challenges in Production
A. Material Limitations
One of the significant challenges in the production of high-voltage capacitors is the availability of high-quality materials. Sourcing materials that meet the stringent requirements for high-voltage applications can be difficult and costly. Additionally, the performance of high-voltage capacitors is often dependent on the quality of the materials used, making it essential for manufacturers to invest in reliable suppliers.
B. Process Optimization
Balancing production speed and quality is another challenge faced by manufacturers. While increasing production rates can lead to cost savings, it may also compromise the quality of the final product. Manufacturers must continuously seek ways to optimize their processes, reduce waste, and improve efficiency without sacrificing quality.
C. Technological Advancements
The integration of automation and robotics in the production process presents both opportunities and challenges. While these technologies can enhance efficiency and precision, they also require significant investment and expertise. Additionally, staying abreast of innovations in materials and design is essential for manufacturers to remain competitive in the market.
VI. Future Trends in High-Voltage Capacitor Production
A. Emerging Materials and Technologies
The future of high-voltage capacitor production is likely to be shaped by emerging materials and technologies. Nanomaterials, for example, hold great potential for enhancing the performance of capacitors, offering improved dielectric properties and energy density. Advances in dielectric materials, such as high-k dielectrics, may also lead to more compact and efficient capacitor designs.
B. Sustainability in Production
Sustainability is becoming increasingly important in the production of high-voltage capacitors. Manufacturers are exploring eco-friendly materials and processes to reduce their environmental impact. Recycling and waste management practices are also gaining attention, as companies seek to minimize waste and promote a circular economy in capacitor production.
C. Market Demand and Applications
The demand for high-voltage capacitors is expected to grow in response to the increasing adoption of renewable energy systems and electric vehicles. As these technologies continue to evolve, the need for reliable and efficient capacitors will become even more critical. Manufacturers must be prepared to adapt to changing market demands and explore new applications for high-voltage capacitors.
VII. Conclusion
High-voltage parallel capacitors play a vital role in modern electrical systems, and understanding their production processes is essential for ensuring their reliability and efficiency. From material selection to assembly and testing, each step in the production process contributes to the overall performance of these components. While challenges such as material limitations and process optimization persist, advancements in technology and a focus on sustainability are shaping the future of high-voltage capacitor manufacturing. As the demand for these components continues to grow, manufacturers must remain agile and innovative to meet the evolving needs of the industry.