Common Production Processes for Capacitor Films
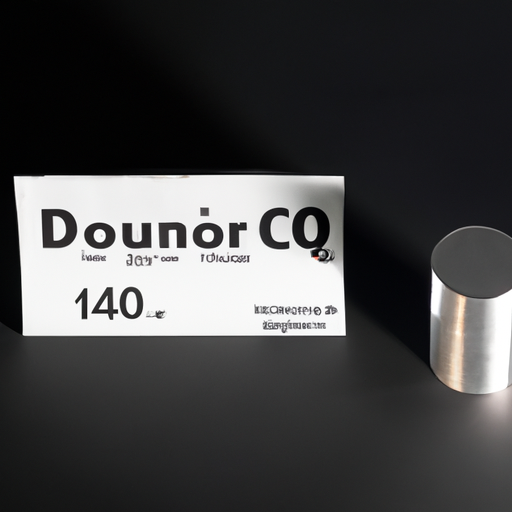
I. Introduction
Capacitor films are essential components in the world of electronics, serving as dielectric materials in capacitors that store and release electrical energy. These films play a crucial role in various applications, from consumer electronics to industrial machinery, making their production processes vital to the electronics industry. Understanding the common production processes for capacitor films not only sheds light on their manufacturing but also highlights the innovations and advancements that continue to shape this field.
II. Types of Capacitor Films
Capacitor films can be categorized into three main types: polymer films, metalized films, and ceramic films. Each type has distinct characteristics and applications.
A. Polymer Films
Polymer films are widely used in capacitors due to their excellent dielectric properties. Common polymers include polypropylene (PP), polyethylene terephthalate (PET), and polyvinylidene fluoride (PVDF). These films are lightweight, flexible, and can be produced in various thicknesses, making them suitable for a range of applications, including audio equipment, power supplies, and automotive electronics.
B. Metalized Films
Metalized films are created by depositing a thin layer of metal onto a polymer film, enhancing its electrical performance. Aluminum and zinc are commonly used metals for this purpose. Metalized films are known for their high capacitance and low equivalent series resistance (ESR), making them ideal for high-frequency applications, such as RF circuits and power electronics.
C. Ceramic Films
Ceramic films, while less common than polymer and metalized films, are used in specific applications where high temperature and voltage stability are required. These films are typically made from materials like barium titanate and are used in applications such as high-voltage capacitors and specialized electronic devices.
III. Raw Materials for Capacitor Films
The production of capacitor films relies on various raw materials, each contributing to the film's performance and characteristics.
A. Types of Polymers Used
1. **Polypropylene (PP)**: Known for its high dielectric strength and low loss factor, PP is a popular choice for capacitor films. It is also resistant to moisture and chemicals, making it suitable for various environments.
2. **Polyethylene (PET)**: PET films offer excellent thermal stability and mechanical strength. They are often used in applications requiring high reliability and durability.
3. **Polyvinylidene Fluoride (PVDF)**: PVDF is known for its high dielectric constant and excellent chemical resistance. It is often used in specialized applications, including high-frequency capacitors.
B. Metal Coatings
1. **Aluminum**: Aluminum is the most commonly used metal for metallization due to its excellent conductivity and cost-effectiveness.
2. **Zinc**: Zinc is sometimes used as an alternative to aluminum, particularly in applications where corrosion resistance is essential.
C. Additives and Fillers
Additives and fillers are often incorporated into the polymer matrix to enhance specific properties, such as thermal stability, mechanical strength, and electrical performance. Common additives include stabilizers, antioxidants, and flame retardants.
IV. Common Production Processes
The production of capacitor films involves several key processes, each with its own set of equipment, advantages, and disadvantages.
A. Film Extrusion
Film extrusion is one of the most common methods for producing polymer films. In this process, raw polymer pellets are melted and forced through a die to form a continuous film.
1. **Overview of the Process**: The molten polymer is extruded through a flat or tubular die, cooled, and then wound onto rolls.
2. **Equipment Used**: Extruders, cooling systems, and winding machines are essential components of the film extrusion process.
3. **Advantages and Disadvantages**: Film extrusion allows for high production rates and uniform thickness. However, it may have limitations in terms of film clarity and surface finish compared to other methods.
B. Film Casting
Film casting involves pouring a polymer solution onto a flat surface and allowing it to evaporate, forming a film.
1. **Overview of the Process**: The polymer solution is spread onto a casting surface, where it is dried to form a thin film.
2. **Equipment Used**: Casting machines, drying ovens, and rollers are used in this process.
3. **Advantages and Disadvantages**: Film casting can produce high-quality films with excellent optical properties. However, it is generally slower than extrusion and may not be suitable for large-scale production.
C. Metallization
Metallization is a critical step in producing metalized films, enhancing their electrical properties.
1. **Physical Vapor Deposition (PVD)**: In PVD, metal is vaporized in a vacuum and deposited onto the film surface. This method provides a uniform coating and excellent adhesion.
2. **Chemical Vapor Deposition (CVD)**: CVD involves chemical reactions that deposit metal onto the film. This method can produce high-purity coatings but may require more complex equipment.
3. **Advantages and Disadvantages**: Metallization improves capacitance and reduces ESR. However, the processes can be costly and require precise control to ensure uniformity.
D. Lamination
Lamination involves bonding multiple layers of films together to enhance their properties.
1. **Overview of the Process**: Two or more films are bonded using heat, pressure, or adhesives to create a composite film.
2. **Equipment Used**: Laminating machines and rollers are used in this process.
3. **Advantages and Disadvantages**: Lamination can improve mechanical strength and dielectric properties. However, it may increase production complexity and costs.
E. Slitting and Cutting
Slitting and cutting are essential final steps in the production process, ensuring that the films are of the desired size and shape.
1. **Overview of the Process**: Large rolls of film are cut into smaller widths or specific shapes as required by the application.
2. **Equipment Used**: Slitting machines and cutting tools are used in this process.
3. **Importance in the Production Line**: Proper slitting and cutting are crucial for ensuring that the films meet specifications and can be easily integrated into capacitor assemblies.
V. Quality Control Measures
Quality control is paramount in the production of capacitor films to ensure reliability and performance.
A. Testing Methods for Capacitor Films
1. **Electrical Testing**: This includes measuring capacitance, ESR, and dielectric strength to ensure the films meet electrical specifications.
2. **Mechanical Testing**: Mechanical properties such as tensile strength and elongation are tested to ensure the films can withstand handling and application stresses.
3. **Thermal Testing**: Thermal stability is assessed to ensure the films can operate effectively under varying temperature conditions.
B. Standards and Certifications
1. **ISO Standards**: Compliance with ISO standards ensures that production processes meet international quality management criteria.
2. **Industry-Specific Certifications**: Certifications such as UL and RoHS ensure that the films meet safety and environmental regulations.
VI. Innovations and Future Trends
The capacitor film industry is continuously evolving, driven by advancements in materials science and production technologies.
A. Advances in Materials Science
Research into new polymer blends and composites is leading to the development of films with enhanced properties, such as higher capacitance and improved thermal stability.
B. Eco-Friendly Production Processes
Sustainability is becoming increasingly important, with manufacturers exploring eco-friendly materials and production methods to reduce environmental impact.
C. Emerging Technologies in Capacitor Film Production
Innovations such as nanotechnology and 3D printing are being explored to create films with tailored properties for specific applications, potentially revolutionizing the industry.
VII. Conclusion
In summary, the production processes for capacitor films are diverse and complex, involving various materials and methods. Understanding these processes is crucial for manufacturers and engineers alike, as it impacts the performance and reliability of electronic components. As the industry continues to innovate, the future of capacitor film production looks promising, with advancements in materials and eco-friendly practices paving the way for more efficient and sustainable manufacturing.
VIII. References
1. Academic journals on materials science and electronics.
2. Industry reports on capacitor technology and production trends.
3. Manufacturer guidelines and specifications for capacitor films.
This comprehensive overview of the common production processes for capacitor films highlights the importance of each step in ensuring high-quality electronic components. As technology advances, staying informed about these processes will be essential for anyone involved in the electronics industry.
Common Production Processes for Capacitor Films
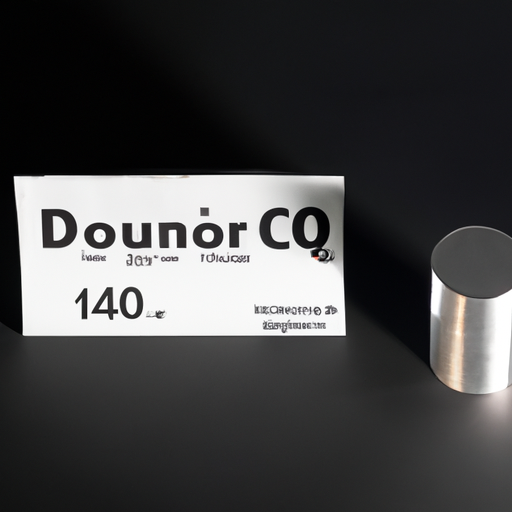
I. Introduction
Capacitor films are essential components in the world of electronics, serving as dielectric materials in capacitors that store and release electrical energy. These films play a crucial role in various applications, from consumer electronics to industrial machinery, making their production processes vital to the electronics industry. Understanding the common production processes for capacitor films not only sheds light on their manufacturing but also highlights the innovations and advancements that continue to shape this field.
II. Types of Capacitor Films
Capacitor films can be categorized into three main types: polymer films, metalized films, and ceramic films. Each type has distinct characteristics and applications.
A. Polymer Films
Polymer films are widely used in capacitors due to their excellent dielectric properties. Common polymers include polypropylene (PP), polyethylene terephthalate (PET), and polyvinylidene fluoride (PVDF). These films are lightweight, flexible, and can be produced in various thicknesses, making them suitable for a range of applications, including audio equipment, power supplies, and automotive electronics.
B. Metalized Films
Metalized films are created by depositing a thin layer of metal onto a polymer film, enhancing its electrical performance. Aluminum and zinc are commonly used metals for this purpose. Metalized films are known for their high capacitance and low equivalent series resistance (ESR), making them ideal for high-frequency applications, such as RF circuits and power electronics.
C. Ceramic Films
Ceramic films, while less common than polymer and metalized films, are used in specific applications where high temperature and voltage stability are required. These films are typically made from materials like barium titanate and are used in applications such as high-voltage capacitors and specialized electronic devices.
III. Raw Materials for Capacitor Films
The production of capacitor films relies on various raw materials, each contributing to the film's performance and characteristics.
A. Types of Polymers Used
1. **Polypropylene (PP)**: Known for its high dielectric strength and low loss factor, PP is a popular choice for capacitor films. It is also resistant to moisture and chemicals, making it suitable for various environments.
2. **Polyethylene (PET)**: PET films offer excellent thermal stability and mechanical strength. They are often used in applications requiring high reliability and durability.
3. **Polyvinylidene Fluoride (PVDF)**: PVDF is known for its high dielectric constant and excellent chemical resistance. It is often used in specialized applications, including high-frequency capacitors.
B. Metal Coatings
1. **Aluminum**: Aluminum is the most commonly used metal for metallization due to its excellent conductivity and cost-effectiveness.
2. **Zinc**: Zinc is sometimes used as an alternative to aluminum, particularly in applications where corrosion resistance is essential.
C. Additives and Fillers
Additives and fillers are often incorporated into the polymer matrix to enhance specific properties, such as thermal stability, mechanical strength, and electrical performance. Common additives include stabilizers, antioxidants, and flame retardants.
IV. Common Production Processes
The production of capacitor films involves several key processes, each with its own set of equipment, advantages, and disadvantages.
A. Film Extrusion
Film extrusion is one of the most common methods for producing polymer films. In this process, raw polymer pellets are melted and forced through a die to form a continuous film.
1. **Overview of the Process**: The molten polymer is extruded through a flat or tubular die, cooled, and then wound onto rolls.
2. **Equipment Used**: Extruders, cooling systems, and winding machines are essential components of the film extrusion process.
3. **Advantages and Disadvantages**: Film extrusion allows for high production rates and uniform thickness. However, it may have limitations in terms of film clarity and surface finish compared to other methods.
B. Film Casting
Film casting involves pouring a polymer solution onto a flat surface and allowing it to evaporate, forming a film.
1. **Overview of the Process**: The polymer solution is spread onto a casting surface, where it is dried to form a thin film.
2. **Equipment Used**: Casting machines, drying ovens, and rollers are used in this process.
3. **Advantages and Disadvantages**: Film casting can produce high-quality films with excellent optical properties. However, it is generally slower than extrusion and may not be suitable for large-scale production.
C. Metallization
Metallization is a critical step in producing metalized films, enhancing their electrical properties.
1. **Physical Vapor Deposition (PVD)**: In PVD, metal is vaporized in a vacuum and deposited onto the film surface. This method provides a uniform coating and excellent adhesion.
2. **Chemical Vapor Deposition (CVD)**: CVD involves chemical reactions that deposit metal onto the film. This method can produce high-purity coatings but may require more complex equipment.
3. **Advantages and Disadvantages**: Metallization improves capacitance and reduces ESR. However, the processes can be costly and require precise control to ensure uniformity.
D. Lamination
Lamination involves bonding multiple layers of films together to enhance their properties.
1. **Overview of the Process**: Two or more films are bonded using heat, pressure, or adhesives to create a composite film.
2. **Equipment Used**: Laminating machines and rollers are used in this process.
3. **Advantages and Disadvantages**: Lamination can improve mechanical strength and dielectric properties. However, it may increase production complexity and costs.
E. Slitting and Cutting
Slitting and cutting are essential final steps in the production process, ensuring that the films are of the desired size and shape.
1. **Overview of the Process**: Large rolls of film are cut into smaller widths or specific shapes as required by the application.
2. **Equipment Used**: Slitting machines and cutting tools are used in this process.
3. **Importance in the Production Line**: Proper slitting and cutting are crucial for ensuring that the films meet specifications and can be easily integrated into capacitor assemblies.
V. Quality Control Measures
Quality control is paramount in the production of capacitor films to ensure reliability and performance.
A. Testing Methods for Capacitor Films
1. **Electrical Testing**: This includes measuring capacitance, ESR, and dielectric strength to ensure the films meet electrical specifications.
2. **Mechanical Testing**: Mechanical properties such as tensile strength and elongation are tested to ensure the films can withstand handling and application stresses.
3. **Thermal Testing**: Thermal stability is assessed to ensure the films can operate effectively under varying temperature conditions.
B. Standards and Certifications
1. **ISO Standards**: Compliance with ISO standards ensures that production processes meet international quality management criteria.
2. **Industry-Specific Certifications**: Certifications such as UL and RoHS ensure that the films meet safety and environmental regulations.
VI. Innovations and Future Trends
The capacitor film industry is continuously evolving, driven by advancements in materials science and production technologies.
A. Advances in Materials Science
Research into new polymer blends and composites is leading to the development of films with enhanced properties, such as higher capacitance and improved thermal stability.
B. Eco-Friendly Production Processes
Sustainability is becoming increasingly important, with manufacturers exploring eco-friendly materials and production methods to reduce environmental impact.
C. Emerging Technologies in Capacitor Film Production
Innovations such as nanotechnology and 3D printing are being explored to create films with tailored properties for specific applications, potentially revolutionizing the industry.
VII. Conclusion
In summary, the production processes for capacitor films are diverse and complex, involving various materials and methods. Understanding these processes is crucial for manufacturers and engineers alike, as it impacts the performance and reliability of electronic components. As the industry continues to innovate, the future of capacitor film production looks promising, with advancements in materials and eco-friendly practices paving the way for more efficient and sustainable manufacturing.
VIII. References
1. Academic journals on materials science and electronics.
2. Industry reports on capacitor technology and production trends.
3. Manufacturer guidelines and specifications for capacitor films.
This comprehensive overview of the common production processes for capacitor films highlights the importance of each step in ensuring high-quality electronic components. As technology advances, staying informed about these processes will be essential for anyone involved in the electronics industry.