What are the Product Standards of Capacitor Companies?
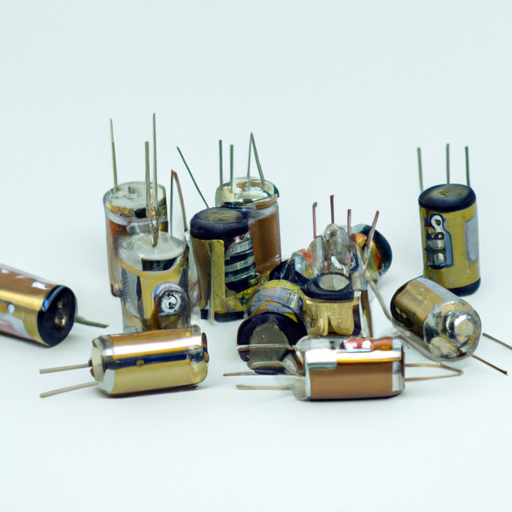
I. Introduction
Capacitors are essential components in electronic circuits, serving as energy storage devices that can release energy quickly when needed. They play a critical role in various applications, from power supply systems to signal processing. Given their importance, the standards governing the production and performance of capacitors are crucial for ensuring quality, safety, and reliability in electronic devices. This article aims to explore the product standards of capacitor companies, detailing the relevant organizations, types of capacitors, testing methods, compliance requirements, and future trends in capacitor standards.
II. Understanding Capacitor Standards
A. Definition of Product Standards
Product standards are established criteria that define the quality, safety, and performance requirements for products. In the capacitor industry, these standards ensure that capacitors meet specific performance metrics and safety regulations, thereby protecting consumers and manufacturers alike.
B. Role of Standards in Ensuring Quality and Safety
Standards play a vital role in maintaining the integrity of capacitors. They help manufacturers produce reliable products that can withstand various operating conditions, ensuring that capacitors perform as expected in their intended applications. Compliance with these standards also minimizes the risk of product failures, which can lead to safety hazards and financial losses.
C. Types of Standards Relevant to Capacitors
Capacitor standards can be categorized into several types, including performance standards, safety standards, and environmental standards. Performance standards dictate the electrical characteristics of capacitors, while safety standards focus on preventing hazards associated with capacitor failure. Environmental standards, such as RoHS (Restriction of Hazardous Substances), ensure that capacitors are manufactured without harmful materials.
III. Key Organizations and Regulatory Bodies
A. International Electrotechnical Commission (IEC)
1. Overview of IEC
The IEC is a global organization that develops and publishes international standards for electrical and electronic technologies. It plays a crucial role in ensuring that electrical products, including capacitors, are safe and reliable.
2. Relevant IEC Standards for Capacitors
IEC standards relevant to capacitors include IEC 60384, which outlines the requirements for fixed capacitors for use in electronic equipment. This standard covers aspects such as electrical performance, mechanical properties, and safety requirements.
B. Institute of Electrical and Electronics Engineers (IEEE)
1. Overview of IEEE
IEEE is a leading organization in the development of standards for electrical and electronic systems. It focuses on advancing technology for humanity and has a significant influence on the standards applicable to capacitors.
2. IEEE Standards Applicable to Capacitors
IEEE standards, such as IEEE 18, provide guidelines for the testing and performance of capacitors used in power systems. These standards help ensure that capacitors can handle the electrical stresses encountered in high-voltage applications.
C. Underwriters Laboratories (UL)
1. Overview of UL
UL is a global safety certification organization that tests and certifies products for safety and performance. Its certification is often a requirement for manufacturers looking to market their products in various regions.
2. UL Certification Process for Capacitors
The UL certification process involves rigorous testing of capacitors to ensure they meet safety standards. This includes evaluating the capacitor's construction, materials, and performance under various conditions.
D. Other Relevant Organizations
In addition to IEC, IEEE, and UL, other organizations such as RoHS and REACH (Registration, Evaluation, Authorisation, and Restriction of Chemicals) play a significant role in regulating the materials used in capacitor manufacturing, ensuring that they are environmentally friendly and safe for consumers.
IV. Types of Capacitors and Their Standards
A. Ceramic Capacitors
1. Common Standards and Specifications
Ceramic capacitors are widely used in electronic circuits due to their small size and reliability. Common standards for ceramic capacitors include IEC 60384-14, which specifies the requirements for ceramic dielectric capacitors.
2. Applications and Implications of Standards
The standards governing ceramic capacitors ensure that they can operate effectively in various applications, from consumer electronics to industrial machinery. Compliance with these standards is crucial for maintaining performance and reliability.
B. Electrolytic Capacitors
1. Key Standards and Testing Methods
Electrolytic capacitors are known for their high capacitance values and are commonly used in power supply applications. Standards such as IEC 60384-4 outline the performance and safety requirements for these capacitors.
2. Importance of Standards in Reliability
The reliability of electrolytic capacitors is heavily influenced by adherence to standards. These standards dictate testing methods for parameters such as leakage current and equivalent series resistance (ESR), which are critical for ensuring long-term performance.
C. Film Capacitors
1. Standards Governing Film Capacitors
Film capacitors are known for their stability and low losses. Standards such as IEC 60384-17 provide guidelines for the performance and safety of film capacitors, ensuring they meet the necessary quality benchmarks.
2. Impact of Standards on Performance
Compliance with these standards directly impacts the performance of film capacitors, making them suitable for applications requiring high precision and reliability, such as audio equipment and power electronics.
D. Tantalum Capacitors
1. Specific Standards for Tantalum Capacitors
Tantalum capacitors are used in applications where high capacitance and reliability are required. Standards such as IEC 60384-20 outline the requirements for tantalum capacitors, focusing on their performance and safety.
2. Safety and Reliability Considerations
Given the potential risks associated with tantalum capacitors, such as thermal runaway, adherence to safety standards is critical. These standards help mitigate risks and ensure that tantalum capacitors perform reliably in demanding applications.
V. Testing and Quality Assurance
A. Importance of Testing in Capacitor Manufacturing
Testing is a fundamental aspect of capacitor manufacturing, ensuring that products meet the required standards and specifications. Rigorous testing helps identify defects and ensures that capacitors perform reliably in their intended applications.
B. Common Testing Methods and Procedures
1. Voltage Testing
Voltage testing assesses a capacitor's ability to withstand electrical stress without failure. This test is crucial for ensuring that capacitors can operate safely in high-voltage environments.
2. Capacitance Measurement
Capacitance measurement determines the actual capacitance value of a capacitor, ensuring it meets the specified requirements. This measurement is essential for maintaining performance in electronic circuits.
3. ESR (Equivalent Series Resistance) Testing
ESR testing evaluates the internal resistance of a capacitor, which affects its efficiency and performance. Low ESR values are desirable for high-frequency applications, making this test critical for ensuring reliability.
C. Quality Assurance Processes in Capacitor Companies
1. In-Process Quality Control
In-process quality control involves monitoring the manufacturing process to identify and rectify defects early. This proactive approach helps maintain product quality and reduces waste.
2. Final Product Testing
Final product testing ensures that capacitors meet all specified standards before they are shipped to customers. This testing phase is crucial for maintaining the reputation of capacitor manufacturers and ensuring customer satisfaction.
VI. Compliance and Certification
A. Importance of Compliance with International Standards
Compliance with international standards is essential for capacitor manufacturers to ensure their products are safe, reliable, and marketable. Adhering to these standards helps build trust with customers and regulatory bodies.
B. Certification Processes for Capacitor Manufacturers
The certification process typically involves rigorous testing and evaluation by recognized organizations. Manufacturers must demonstrate that their products meet the necessary standards to obtain certification, which can enhance their marketability.
C. Consequences of Non-Compliance
Non-compliance with product standards can lead to severe consequences, including product recalls, legal liabilities, and damage to a manufacturer's reputation. Ensuring compliance is therefore critical for the long-term success of capacitor companies.
VII. Challenges in Meeting Product Standards
A. Technological Advancements and Evolving Standards
As technology advances, product standards must evolve to keep pace with new developments. This can pose challenges for manufacturers, who must continuously adapt their processes and products to meet changing requirements.
B. Globalization and Varying Regional Standards
Globalization has led to a diverse market with varying regional standards. Manufacturers must navigate these differences to ensure compliance in multiple markets, which can complicate production and increase costs.
C. Balancing Cost and Compliance
Manufacturers often face the challenge of balancing the costs associated with compliance and the need to remain competitive. Finding cost-effective solutions while adhering to standards is crucial for maintaining profitability.
VIII. Future Trends in Capacitor Standards
A. Emerging Technologies and Their Impact on Standards
Emerging technologies, such as electric vehicles and renewable energy systems, are driving the need for new capacitor standards. As these technologies evolve, standards will need to adapt to ensure safety and performance.
B. Sustainability and Environmental Considerations
Sustainability is becoming increasingly important in the capacitor industry. Manufacturers are being urged to adopt environmentally friendly practices and materials, leading to the development of new standards focused on sustainability.
C. Predictions for Future Standard Developments
As the industry continues to evolve, we can expect to see more comprehensive standards that address emerging technologies, sustainability, and safety. These developments will be crucial for ensuring the continued reliability and safety of capacitors in various applications.
IX. Conclusion
In conclusion, product standards play a vital role in the capacitor industry, ensuring that capacitors are safe, reliable, and perform as expected. Compliance with these standards is essential for manufacturers to maintain their reputation and meet customer expectations. As technology continues to advance, the importance of adhering to evolving standards will only increase. Manufacturers and consumers alike must prioritize compliance and quality to ensure the continued success of the capacitor industry.
X. References
- International Electrotechnical Commission (IEC) Standards
- Institute of Electrical and Electronics Engineers (IEEE) Standards
- Underwriters Laboratories (UL) Certification Guidelines
- RoHS and REACH Regulations
- Various industry publications and technical papers on capacitor standards and testing methods.
This comprehensive overview of capacitor product standards highlights the importance of quality and safety in the industry, providing valuable insights for manufacturers and consumers alike.
What are the Product Standards of Capacitor Companies?
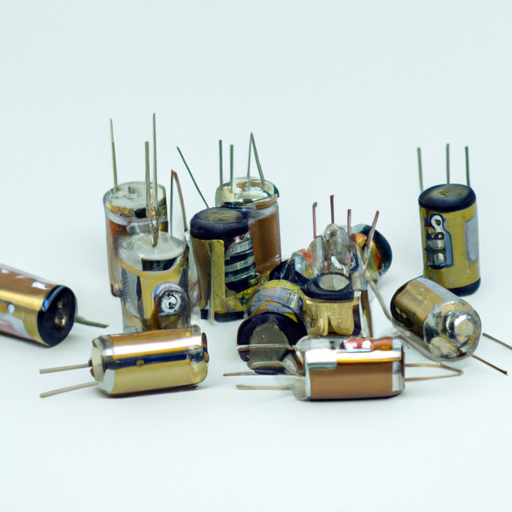
I. Introduction
Capacitors are essential components in electronic circuits, serving as energy storage devices that can release energy quickly when needed. They play a critical role in various applications, from power supply systems to signal processing. Given their importance, the standards governing the production and performance of capacitors are crucial for ensuring quality, safety, and reliability in electronic devices. This article aims to explore the product standards of capacitor companies, detailing the relevant organizations, types of capacitors, testing methods, compliance requirements, and future trends in capacitor standards.
II. Understanding Capacitor Standards
A. Definition of Product Standards
Product standards are established criteria that define the quality, safety, and performance requirements for products. In the capacitor industry, these standards ensure that capacitors meet specific performance metrics and safety regulations, thereby protecting consumers and manufacturers alike.
B. Role of Standards in Ensuring Quality and Safety
Standards play a vital role in maintaining the integrity of capacitors. They help manufacturers produce reliable products that can withstand various operating conditions, ensuring that capacitors perform as expected in their intended applications. Compliance with these standards also minimizes the risk of product failures, which can lead to safety hazards and financial losses.
C. Types of Standards Relevant to Capacitors
Capacitor standards can be categorized into several types, including performance standards, safety standards, and environmental standards. Performance standards dictate the electrical characteristics of capacitors, while safety standards focus on preventing hazards associated with capacitor failure. Environmental standards, such as RoHS (Restriction of Hazardous Substances), ensure that capacitors are manufactured without harmful materials.
III. Key Organizations and Regulatory Bodies
A. International Electrotechnical Commission (IEC)
1. Overview of IEC
The IEC is a global organization that develops and publishes international standards for electrical and electronic technologies. It plays a crucial role in ensuring that electrical products, including capacitors, are safe and reliable.
2. Relevant IEC Standards for Capacitors
IEC standards relevant to capacitors include IEC 60384, which outlines the requirements for fixed capacitors for use in electronic equipment. This standard covers aspects such as electrical performance, mechanical properties, and safety requirements.
B. Institute of Electrical and Electronics Engineers (IEEE)
1. Overview of IEEE
IEEE is a leading organization in the development of standards for electrical and electronic systems. It focuses on advancing technology for humanity and has a significant influence on the standards applicable to capacitors.
2. IEEE Standards Applicable to Capacitors
IEEE standards, such as IEEE 18, provide guidelines for the testing and performance of capacitors used in power systems. These standards help ensure that capacitors can handle the electrical stresses encountered in high-voltage applications.
C. Underwriters Laboratories (UL)
1. Overview of UL
UL is a global safety certification organization that tests and certifies products for safety and performance. Its certification is often a requirement for manufacturers looking to market their products in various regions.
2. UL Certification Process for Capacitors
The UL certification process involves rigorous testing of capacitors to ensure they meet safety standards. This includes evaluating the capacitor's construction, materials, and performance under various conditions.
D. Other Relevant Organizations
In addition to IEC, IEEE, and UL, other organizations such as RoHS and REACH (Registration, Evaluation, Authorisation, and Restriction of Chemicals) play a significant role in regulating the materials used in capacitor manufacturing, ensuring that they are environmentally friendly and safe for consumers.
IV. Types of Capacitors and Their Standards
A. Ceramic Capacitors
1. Common Standards and Specifications
Ceramic capacitors are widely used in electronic circuits due to their small size and reliability. Common standards for ceramic capacitors include IEC 60384-14, which specifies the requirements for ceramic dielectric capacitors.
2. Applications and Implications of Standards
The standards governing ceramic capacitors ensure that they can operate effectively in various applications, from consumer electronics to industrial machinery. Compliance with these standards is crucial for maintaining performance and reliability.
B. Electrolytic Capacitors
1. Key Standards and Testing Methods
Electrolytic capacitors are known for their high capacitance values and are commonly used in power supply applications. Standards such as IEC 60384-4 outline the performance and safety requirements for these capacitors.
2. Importance of Standards in Reliability
The reliability of electrolytic capacitors is heavily influenced by adherence to standards. These standards dictate testing methods for parameters such as leakage current and equivalent series resistance (ESR), which are critical for ensuring long-term performance.
C. Film Capacitors
1. Standards Governing Film Capacitors
Film capacitors are known for their stability and low losses. Standards such as IEC 60384-17 provide guidelines for the performance and safety of film capacitors, ensuring they meet the necessary quality benchmarks.
2. Impact of Standards on Performance
Compliance with these standards directly impacts the performance of film capacitors, making them suitable for applications requiring high precision and reliability, such as audio equipment and power electronics.
D. Tantalum Capacitors
1. Specific Standards for Tantalum Capacitors
Tantalum capacitors are used in applications where high capacitance and reliability are required. Standards such as IEC 60384-20 outline the requirements for tantalum capacitors, focusing on their performance and safety.
2. Safety and Reliability Considerations
Given the potential risks associated with tantalum capacitors, such as thermal runaway, adherence to safety standards is critical. These standards help mitigate risks and ensure that tantalum capacitors perform reliably in demanding applications.
V. Testing and Quality Assurance
A. Importance of Testing in Capacitor Manufacturing
Testing is a fundamental aspect of capacitor manufacturing, ensuring that products meet the required standards and specifications. Rigorous testing helps identify defects and ensures that capacitors perform reliably in their intended applications.
B. Common Testing Methods and Procedures
1. Voltage Testing
Voltage testing assesses a capacitor's ability to withstand electrical stress without failure. This test is crucial for ensuring that capacitors can operate safely in high-voltage environments.
2. Capacitance Measurement
Capacitance measurement determines the actual capacitance value of a capacitor, ensuring it meets the specified requirements. This measurement is essential for maintaining performance in electronic circuits.
3. ESR (Equivalent Series Resistance) Testing
ESR testing evaluates the internal resistance of a capacitor, which affects its efficiency and performance. Low ESR values are desirable for high-frequency applications, making this test critical for ensuring reliability.
C. Quality Assurance Processes in Capacitor Companies
1. In-Process Quality Control
In-process quality control involves monitoring the manufacturing process to identify and rectify defects early. This proactive approach helps maintain product quality and reduces waste.
2. Final Product Testing
Final product testing ensures that capacitors meet all specified standards before they are shipped to customers. This testing phase is crucial for maintaining the reputation of capacitor manufacturers and ensuring customer satisfaction.
VI. Compliance and Certification
A. Importance of Compliance with International Standards
Compliance with international standards is essential for capacitor manufacturers to ensure their products are safe, reliable, and marketable. Adhering to these standards helps build trust with customers and regulatory bodies.
B. Certification Processes for Capacitor Manufacturers
The certification process typically involves rigorous testing and evaluation by recognized organizations. Manufacturers must demonstrate that their products meet the necessary standards to obtain certification, which can enhance their marketability.
C. Consequences of Non-Compliance
Non-compliance with product standards can lead to severe consequences, including product recalls, legal liabilities, and damage to a manufacturer's reputation. Ensuring compliance is therefore critical for the long-term success of capacitor companies.
VII. Challenges in Meeting Product Standards
A. Technological Advancements and Evolving Standards
As technology advances, product standards must evolve to keep pace with new developments. This can pose challenges for manufacturers, who must continuously adapt their processes and products to meet changing requirements.
B. Globalization and Varying Regional Standards
Globalization has led to a diverse market with varying regional standards. Manufacturers must navigate these differences to ensure compliance in multiple markets, which can complicate production and increase costs.
C. Balancing Cost and Compliance
Manufacturers often face the challenge of balancing the costs associated with compliance and the need to remain competitive. Finding cost-effective solutions while adhering to standards is crucial for maintaining profitability.
VIII. Future Trends in Capacitor Standards
A. Emerging Technologies and Their Impact on Standards
Emerging technologies, such as electric vehicles and renewable energy systems, are driving the need for new capacitor standards. As these technologies evolve, standards will need to adapt to ensure safety and performance.
B. Sustainability and Environmental Considerations
Sustainability is becoming increasingly important in the capacitor industry. Manufacturers are being urged to adopt environmentally friendly practices and materials, leading to the development of new standards focused on sustainability.
C. Predictions for Future Standard Developments
As the industry continues to evolve, we can expect to see more comprehensive standards that address emerging technologies, sustainability, and safety. These developments will be crucial for ensuring the continued reliability and safety of capacitors in various applications.
IX. Conclusion
In conclusion, product standards play a vital role in the capacitor industry, ensuring that capacitors are safe, reliable, and perform as expected. Compliance with these standards is essential for manufacturers to maintain their reputation and meet customer expectations. As technology continues to advance, the importance of adhering to evolving standards will only increase. Manufacturers and consumers alike must prioritize compliance and quality to ensure the continued success of the capacitor industry.
X. References
- International Electrotechnical Commission (IEC) Standards
- Institute of Electrical and Electronics Engineers (IEEE) Standards
- Underwriters Laboratories (UL) Certification Guidelines
- RoHS and REACH Regulations
- Various industry publications and technical papers on capacitor standards and testing methods.
This comprehensive overview of capacitor product standards highlights the importance of quality and safety in the industry, providing valuable insights for manufacturers and consumers alike.