What are the Product Standards for Resistor Packaging?
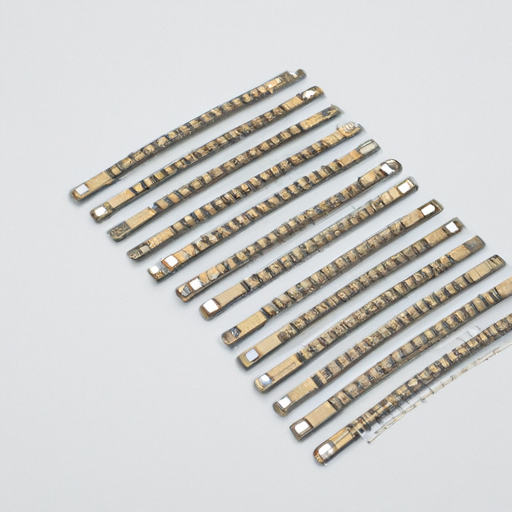
I. Introduction
Resistors are fundamental components in electronic circuits, serving the critical function of controlling current flow and voltage levels. Their importance cannot be overstated, as they play a vital role in ensuring the proper operation of electronic devices, from simple gadgets to complex machinery. However, the performance and reliability of resistors are not solely determined by their electrical characteristics; the packaging in which they are housed is equally crucial. This article aims to explore the product standards for resistor packaging, shedding light on the various types of packaging, relevant standards, material considerations, testing protocols, and future trends.
II. Understanding Resistor Packaging
A. Types of Resistor Packaging
Resistor packaging comes in various forms, each designed to meet specific application requirements:
1. **Through-hole Resistors**: These resistors are designed for insertion into a printed circuit board (PCB) through pre-drilled holes. They are typically larger and provide robust mechanical stability, making them suitable for high-power applications.
2. **Surface-mount Resistors**: These resistors are mounted directly onto the surface of a PCB, allowing for a more compact design. They are widely used in modern electronics due to their space-saving advantages and compatibility with automated assembly processes.
3. **Chip Resistors**: A subtype of surface-mount resistors, chip resistors are small, rectangular components that are ideal for high-density applications. Their minimal size and weight make them popular in portable devices.
B. Importance of Packaging in Electrical Performance
The packaging of resistors plays a significant role in their overall performance:
1. **Thermal Management**: Effective packaging helps dissipate heat generated during operation, preventing overheating and ensuring reliable performance.
2. **Mechanical Stability**: Robust packaging protects resistors from physical stress and vibration, which can lead to failure in demanding environments.
3. **Environmental Protection**: Packaging materials shield resistors from moisture, dust, and other contaminants, enhancing their longevity and reliability.
III. Key Product Standards for Resistor Packaging
A. International Standards
Several international standards govern resistor packaging, ensuring consistency and quality across the industry:
1. **IEC (International Electrotechnical Commission)**:
- **IEC 60115**: This standard outlines the requirements for fixed resistors used in electronic equipment, covering aspects such as electrical performance, reliability, and environmental conditions.
- **IEC 60068**: This standard focuses on environmental testing, providing guidelines for assessing the resilience of resistors to various environmental factors, including temperature, humidity, and mechanical stress.
2. **ISO (International Organization for Standardization)**:
- **ISO 9001**: This standard specifies requirements for quality management systems, ensuring that manufacturers maintain high-quality production processes.
- **ISO 14001**: This standard addresses environmental management systems, promoting sustainable practices in resistor manufacturing.
B. Industry-Specific Standards
In addition to international standards, several industry-specific standards are crucial for resistor packaging:
1. **JEDEC (Joint Electron Device Engineering Council)**:
- **JESD22**: This standard outlines reliability testing methods for electronic components, including resistors, ensuring they meet performance expectations under various conditions.
- **JESD97**: This standard provides guidelines for surface mount technology, addressing the specific requirements for surface-mount resistors.
2. **IPC (Institute for Printed Circuits)**:
- **IPC-A-610**: This standard defines the acceptability criteria for electronic assemblies, ensuring that resistors and other components meet quality standards during assembly.
- **IPC-2221**: This standard offers guidelines for printed board design, which is essential for optimizing resistor placement and performance on PCBs.
IV. Material Standards for Resistor Packaging
A. Common Materials Used in Resistor Packaging
The choice of materials for resistor packaging significantly impacts their performance:
1. **Epoxy Resins**: These materials are commonly used for encapsulating resistors, providing excellent electrical insulation and mechanical protection.
2. **Ceramic Substrates**: Ceramic materials are favored for their thermal stability and electrical insulation properties, making them ideal for high-temperature applications.
3. **Metal Housings**: Metal enclosures offer robust protection against physical damage and environmental factors, enhancing the durability of resistors.
B. Compliance with RoHS and REACH
Manufacturers must ensure that their resistor packaging complies with regulations such as RoHS (Restriction of Hazardous Substances) and REACH (Registration, Evaluation, Authorisation, and Restriction of Chemicals). These regulations aim to minimize the environmental impact of electronic components by restricting the use of hazardous materials.
C. Importance of Material Selection
The selection of materials for resistor packaging is critical for achieving optimal thermal and electrical performance. For instance, materials with high thermal conductivity can help dissipate heat more effectively, while those with excellent electrical insulation properties can prevent short circuits and other failures.
V. Testing and Quality Assurance
A. Importance of Testing in Resistor Packaging
Testing is essential to ensure that resistor packaging meets the required standards and performs reliably in real-world applications:
1. **Electrical Testing**: This involves measuring the resistance, tolerance, and temperature coefficient of resistors to ensure they meet specified performance criteria.
2. **Mechanical Testing**: Mechanical tests assess the physical robustness of resistor packaging, including its ability to withstand vibration, shock, and other stresses.
3. **Environmental Testing**: Environmental tests evaluate how resistors perform under various conditions, such as extreme temperatures, humidity, and exposure to corrosive substances.
B. Common Testing Methods
Several testing methods are commonly employed to assess resistor packaging:
1. **Temperature Cycling**: This test involves subjecting resistors to rapid temperature changes to evaluate their thermal stability and reliability.
2. **Humidity Testing**: This test assesses the performance of resistors in high-humidity environments, ensuring they remain functional and reliable.
3. **Vibration Testing**: This test simulates the mechanical stresses that resistors may encounter during operation, helping to identify potential failure points.
C. Role of Certification Bodies
Certification bodies play a crucial role in ensuring compliance with industry standards. They conduct audits and assessments to verify that manufacturers adhere to established guidelines, providing assurance to customers regarding the quality and reliability of resistor packaging.
VI. Challenges in Resistor Packaging Standards
A. Evolving Technology
As technology continues to advance, the standards governing resistor packaging must also evolve. New materials, manufacturing processes, and design techniques present challenges in maintaining relevant and effective standards.
B. Balancing Performance, Cost, and Environmental Considerations
Manufacturers face the challenge of balancing performance requirements with cost constraints and environmental considerations. Striking this balance is essential for producing high-quality resistors that are also economically viable and environmentally friendly.
C. Continuous Improvement and Innovation
The need for continuous improvement and innovation in packaging solutions is paramount. Manufacturers must stay abreast of emerging technologies and trends to enhance the performance and reliability of resistor packaging.
VII. Future Trends in Resistor Packaging Standards
A. Advances in Materials and Manufacturing Processes
Future trends in resistor packaging will likely see the development of advanced materials that offer improved thermal and electrical performance. Innovations in manufacturing processes, such as additive manufacturing, may also play a role in enhancing packaging solutions.
B. Increased Focus on Sustainability
As environmental concerns grow, there will be an increased focus on sustainability in resistor packaging. Manufacturers will need to adopt eco-friendly practices and materials to meet regulatory requirements and consumer expectations.
C. Role of Automation and Smart Technologies
The integration of automation and smart technologies in quality assurance processes will enhance the efficiency and accuracy of testing and compliance verification. This trend will help manufacturers maintain high standards while reducing production costs.
VIII. Conclusion
In conclusion, product standards for resistor packaging are essential for ensuring the reliability, performance, and safety of electronic components. These standards encompass a wide range of international and industry-specific guidelines that govern various aspects of resistor packaging, from material selection to testing protocols. As technology continues to evolve, manufacturers and engineers must stay informed about emerging standards and practices to ensure that their products meet the demands of modern applications. By prioritizing compliance with these standards, the industry can enhance the quality and reliability of resistors, ultimately contributing to the advancement of electronic technology.
IX. References
- IEC 60115 - Fixed resistors for use in electronic equipment
- IEC 60068 - Environmental testing
- ISO 9001 - Quality management systems
- ISO 14001 - Environmental management systems
- JEDEC JESD22 - Reliability testing
- JEDEC JESD97 - Standard for surface mount technology
- IPC-A-610 - Acceptability of electronic assemblies
- IPC-2221 - Generic standard on printed board design
For further exploration of resistor packaging standards, consider reviewing the latest publications and guidelines from relevant standardization bodies and industry organizations.
What are the Product Standards for Resistor Packaging?
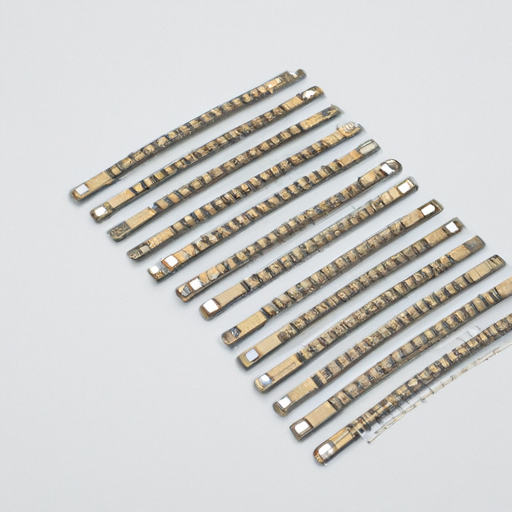
I. Introduction
Resistors are fundamental components in electronic circuits, serving the critical function of controlling current flow and voltage levels. Their importance cannot be overstated, as they play a vital role in ensuring the proper operation of electronic devices, from simple gadgets to complex machinery. However, the performance and reliability of resistors are not solely determined by their electrical characteristics; the packaging in which they are housed is equally crucial. This article aims to explore the product standards for resistor packaging, shedding light on the various types of packaging, relevant standards, material considerations, testing protocols, and future trends.
II. Understanding Resistor Packaging
A. Types of Resistor Packaging
Resistor packaging comes in various forms, each designed to meet specific application requirements:
1. **Through-hole Resistors**: These resistors are designed for insertion into a printed circuit board (PCB) through pre-drilled holes. They are typically larger and provide robust mechanical stability, making them suitable for high-power applications.
2. **Surface-mount Resistors**: These resistors are mounted directly onto the surface of a PCB, allowing for a more compact design. They are widely used in modern electronics due to their space-saving advantages and compatibility with automated assembly processes.
3. **Chip Resistors**: A subtype of surface-mount resistors, chip resistors are small, rectangular components that are ideal for high-density applications. Their minimal size and weight make them popular in portable devices.
B. Importance of Packaging in Electrical Performance
The packaging of resistors plays a significant role in their overall performance:
1. **Thermal Management**: Effective packaging helps dissipate heat generated during operation, preventing overheating and ensuring reliable performance.
2. **Mechanical Stability**: Robust packaging protects resistors from physical stress and vibration, which can lead to failure in demanding environments.
3. **Environmental Protection**: Packaging materials shield resistors from moisture, dust, and other contaminants, enhancing their longevity and reliability.
III. Key Product Standards for Resistor Packaging
A. International Standards
Several international standards govern resistor packaging, ensuring consistency and quality across the industry:
1. **IEC (International Electrotechnical Commission)**:
- **IEC 60115**: This standard outlines the requirements for fixed resistors used in electronic equipment, covering aspects such as electrical performance, reliability, and environmental conditions.
- **IEC 60068**: This standard focuses on environmental testing, providing guidelines for assessing the resilience of resistors to various environmental factors, including temperature, humidity, and mechanical stress.
2. **ISO (International Organization for Standardization)**:
- **ISO 9001**: This standard specifies requirements for quality management systems, ensuring that manufacturers maintain high-quality production processes.
- **ISO 14001**: This standard addresses environmental management systems, promoting sustainable practices in resistor manufacturing.
B. Industry-Specific Standards
In addition to international standards, several industry-specific standards are crucial for resistor packaging:
1. **JEDEC (Joint Electron Device Engineering Council)**:
- **JESD22**: This standard outlines reliability testing methods for electronic components, including resistors, ensuring they meet performance expectations under various conditions.
- **JESD97**: This standard provides guidelines for surface mount technology, addressing the specific requirements for surface-mount resistors.
2. **IPC (Institute for Printed Circuits)**:
- **IPC-A-610**: This standard defines the acceptability criteria for electronic assemblies, ensuring that resistors and other components meet quality standards during assembly.
- **IPC-2221**: This standard offers guidelines for printed board design, which is essential for optimizing resistor placement and performance on PCBs.
IV. Material Standards for Resistor Packaging
A. Common Materials Used in Resistor Packaging
The choice of materials for resistor packaging significantly impacts their performance:
1. **Epoxy Resins**: These materials are commonly used for encapsulating resistors, providing excellent electrical insulation and mechanical protection.
2. **Ceramic Substrates**: Ceramic materials are favored for their thermal stability and electrical insulation properties, making them ideal for high-temperature applications.
3. **Metal Housings**: Metal enclosures offer robust protection against physical damage and environmental factors, enhancing the durability of resistors.
B. Compliance with RoHS and REACH
Manufacturers must ensure that their resistor packaging complies with regulations such as RoHS (Restriction of Hazardous Substances) and REACH (Registration, Evaluation, Authorisation, and Restriction of Chemicals). These regulations aim to minimize the environmental impact of electronic components by restricting the use of hazardous materials.
C. Importance of Material Selection
The selection of materials for resistor packaging is critical for achieving optimal thermal and electrical performance. For instance, materials with high thermal conductivity can help dissipate heat more effectively, while those with excellent electrical insulation properties can prevent short circuits and other failures.
V. Testing and Quality Assurance
A. Importance of Testing in Resistor Packaging
Testing is essential to ensure that resistor packaging meets the required standards and performs reliably in real-world applications:
1. **Electrical Testing**: This involves measuring the resistance, tolerance, and temperature coefficient of resistors to ensure they meet specified performance criteria.
2. **Mechanical Testing**: Mechanical tests assess the physical robustness of resistor packaging, including its ability to withstand vibration, shock, and other stresses.
3. **Environmental Testing**: Environmental tests evaluate how resistors perform under various conditions, such as extreme temperatures, humidity, and exposure to corrosive substances.
B. Common Testing Methods
Several testing methods are commonly employed to assess resistor packaging:
1. **Temperature Cycling**: This test involves subjecting resistors to rapid temperature changes to evaluate their thermal stability and reliability.
2. **Humidity Testing**: This test assesses the performance of resistors in high-humidity environments, ensuring they remain functional and reliable.
3. **Vibration Testing**: This test simulates the mechanical stresses that resistors may encounter during operation, helping to identify potential failure points.
C. Role of Certification Bodies
Certification bodies play a crucial role in ensuring compliance with industry standards. They conduct audits and assessments to verify that manufacturers adhere to established guidelines, providing assurance to customers regarding the quality and reliability of resistor packaging.
VI. Challenges in Resistor Packaging Standards
A. Evolving Technology
As technology continues to advance, the standards governing resistor packaging must also evolve. New materials, manufacturing processes, and design techniques present challenges in maintaining relevant and effective standards.
B. Balancing Performance, Cost, and Environmental Considerations
Manufacturers face the challenge of balancing performance requirements with cost constraints and environmental considerations. Striking this balance is essential for producing high-quality resistors that are also economically viable and environmentally friendly.
C. Continuous Improvement and Innovation
The need for continuous improvement and innovation in packaging solutions is paramount. Manufacturers must stay abreast of emerging technologies and trends to enhance the performance and reliability of resistor packaging.
VII. Future Trends in Resistor Packaging Standards
A. Advances in Materials and Manufacturing Processes
Future trends in resistor packaging will likely see the development of advanced materials that offer improved thermal and electrical performance. Innovations in manufacturing processes, such as additive manufacturing, may also play a role in enhancing packaging solutions.
B. Increased Focus on Sustainability
As environmental concerns grow, there will be an increased focus on sustainability in resistor packaging. Manufacturers will need to adopt eco-friendly practices and materials to meet regulatory requirements and consumer expectations.
C. Role of Automation and Smart Technologies
The integration of automation and smart technologies in quality assurance processes will enhance the efficiency and accuracy of testing and compliance verification. This trend will help manufacturers maintain high standards while reducing production costs.
VIII. Conclusion
In conclusion, product standards for resistor packaging are essential for ensuring the reliability, performance, and safety of electronic components. These standards encompass a wide range of international and industry-specific guidelines that govern various aspects of resistor packaging, from material selection to testing protocols. As technology continues to evolve, manufacturers and engineers must stay informed about emerging standards and practices to ensure that their products meet the demands of modern applications. By prioritizing compliance with these standards, the industry can enhance the quality and reliability of resistors, ultimately contributing to the advancement of electronic technology.
IX. References
- IEC 60115 - Fixed resistors for use in electronic equipment
- IEC 60068 - Environmental testing
- ISO 9001 - Quality management systems
- ISO 14001 - Environmental management systems
- JEDEC JESD22 - Reliability testing
- JEDEC JESD97 - Standard for surface mount technology
- IPC-A-610 - Acceptability of electronic assemblies
- IPC-2221 - Generic standard on printed board design
For further exploration of resistor packaging standards, consider reviewing the latest publications and guidelines from relevant standardization bodies and industry organizations.