What are the Manufacturing Processes of the Latest Resistor 4?
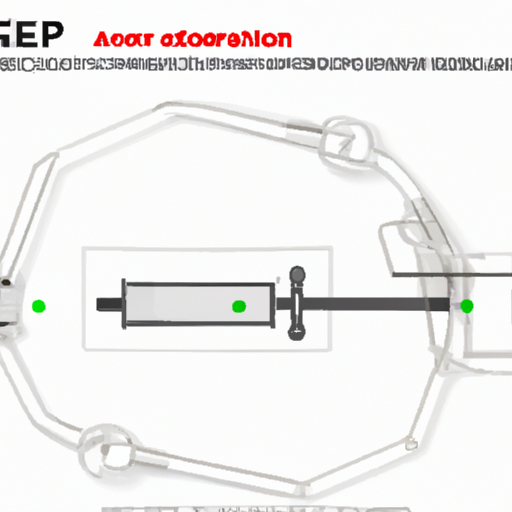
I. Introduction
Resistors are fundamental components in electronic circuits, serving the critical function of controlling current flow. They are essential for protecting sensitive components, dividing voltages, and setting bias points in various applications. Over the years, the evolution of resistors has led to significant advancements in their design and manufacturing processes, culminating in the latest innovation: Resistor 4. This article aims to explore the manufacturing processes behind Resistor 4, highlighting the importance of these processes in enhancing performance and reliability in modern electronics.
II. Understanding Resistor 4
A. Description of Resistor 4 and its Specifications
Resistor 4 represents the latest generation of resistive components, characterized by its high precision, stability, and low temperature coefficient. Typically, Resistor 4 is available in various resistance values, power ratings, and tolerances, making it suitable for a wide range of applications. Its design incorporates advanced materials and manufacturing techniques that contribute to its superior performance compared to earlier resistor models.
B. Applications of Resistor 4 in Modern Electronics
Resistor 4 finds applications across various sectors, including telecommunications, automotive, consumer electronics, and industrial automation. Its high reliability and precision make it ideal for use in critical applications such as signal processing, power management, and sensor interfacing. As electronic devices become more compact and complex, the demand for high-performance resistors like Resistor 4 continues to grow.
C. Importance of Advanced Manufacturing Processes in Enhancing Performance
The performance of Resistor 4 is heavily influenced by the manufacturing processes employed in its production. Advanced techniques ensure that the resistors meet stringent specifications for accuracy, stability, and durability. As technology evolves, the need for innovative manufacturing processes becomes increasingly important to keep pace with the demands of modern electronics.
III. Key Manufacturing Processes
A. Material Selection
1. Types of Materials Used
The choice of materials is crucial in resistor manufacturing. Resistor 4 typically utilizes a variety of materials, including carbon, metal film, and thick film. Each material has unique properties that affect the resistor's performance. For instance, metal film resistors are known for their low noise and high stability, while thick film resistors offer robustness and cost-effectiveness.
2. Importance of Material Properties
Material properties such as temperature coefficient, stability, and resistance tolerance play a significant role in the overall performance of Resistor 4. A low temperature coefficient ensures that the resistor maintains its resistance value across a wide temperature range, which is essential for applications in varying environmental conditions.
B. Design and Engineering
1. Computer-Aided Design (CAD) in Resistor Development
The design phase of Resistor 4 involves the use of computer-aided design (CAD) software to create precise models of the resistor. CAD allows engineers to visualize the resistor's structure and optimize its dimensions for performance. This step is critical in ensuring that the resistor meets the required specifications before moving on to fabrication.
2. Simulation and Modeling for Performance Optimization
Simulation tools are employed to model the electrical behavior of Resistor 4 under different conditions. By simulating various scenarios, engineers can identify potential issues and make necessary adjustments to the design. This iterative process helps in optimizing the resistor's performance and reliability.
C. Fabrication Techniques
1. Thin Film Technology
a. Process Overview
Thin film technology involves depositing a thin layer of resistive material onto a substrate. This process typically uses techniques such as sputtering or chemical vapor deposition (CVD). The thin film is then patterned to create the desired resistance value.
b. Advantages and Applications
Thin film resistors offer high precision and stability, making them suitable for applications in precision instrumentation and high-frequency circuits. Their small size and low parasitic capacitance also make them ideal for compact electronic devices.
2. Thick Film Technology
a. Process Overview
Thick film technology, on the other hand, involves printing a paste of resistive material onto a substrate and then firing it at high temperatures to create a solid layer. This method allows for the production of resistors with higher power ratings and larger physical sizes.
b. Advantages and Applications
Thick film resistors are known for their robustness and cost-effectiveness, making them widely used in consumer electronics and industrial applications. They can handle higher power levels and are less sensitive to environmental factors.
3. Wirewound Resistors
a. Process Overview
Wirewound resistors are made by winding a resistive wire around a core. This method allows for precise control over the resistance value and power rating. The wire is typically made of materials such as nickel-chromium or copper-nickel alloys.
b. Advantages and Applications
Wirewound resistors are known for their high power handling capabilities and excellent stability. They are commonly used in applications requiring high precision and reliability, such as power supplies and audio equipment.
D. Assembly and Packaging
1. Steps in Assembling Resistors
The assembly of Resistor 4 involves several steps, including attaching leads, soldering, and testing. Each step is performed with precision to ensure that the final product meets quality standards.
2. Importance of Packaging in Performance and Reliability
Packaging plays a crucial role in protecting resistors from environmental factors such as moisture, dust, and mechanical stress. The choice of packaging material and design can significantly impact the resistor's performance and longevity.
3. Innovations in Packaging Technology
Recent advancements in packaging technology have led to the development of more compact and efficient designs. Innovations such as surface-mount technology (SMT) allow for easier integration into modern electronic circuits, enhancing the overall performance of Resistor 4.
IV. Quality Control and Testing
A. Importance of Quality Assurance in Resistor Manufacturing
Quality assurance is a critical aspect of resistor manufacturing. Ensuring that each resistor meets the required specifications is essential for maintaining reliability and performance in electronic circuits.
B. Testing Methods for Performance Evaluation
1. Electrical Testing
Electrical testing involves measuring the resistance value, tolerance, and temperature coefficient of the resistor. These tests ensure that the resistor performs as expected under various conditions.
2. Environmental Testing
Environmental testing evaluates the resistor's performance under different environmental conditions, such as temperature extremes and humidity. This testing is crucial for applications where resistors may be exposed to harsh conditions.
C. Standards and Certifications
Manufacturers of Resistor 4 must adhere to various standards and certifications, such as ISO and RoHS. These certifications ensure that the resistors meet international quality and safety standards, providing assurance to customers regarding their reliability.
V. Innovations and Future Trends
A. Emerging Technologies in Resistor Manufacturing
The resistor manufacturing industry is witnessing the emergence of new technologies, such as nanomaterials and advanced ceramics. These materials offer the potential for even higher performance and reliability in resistors.
B. The Role of Automation and Industry 4.0
Automation and Industry 4.0 are transforming the manufacturing landscape, enabling more efficient production processes and improved quality control. Smart manufacturing techniques allow for real-time monitoring and adjustments, enhancing the overall efficiency of resistor production.
C. Future Challenges and Opportunities in Resistor Design and Manufacturing
As electronic devices continue to evolve, resistor manufacturers face challenges such as miniaturization and increased performance demands. However, these challenges also present opportunities for innovation and the development of new resistor technologies that can meet the needs of future applications.
VI. Conclusion
In conclusion, the manufacturing processes of Resistor 4 play a vital role in its performance and reliability in modern electronics. From material selection to advanced fabrication techniques, each step in the manufacturing process contributes to the overall quality of the resistor. As technology continues to advance, the importance of continuous innovation in resistor manufacturing cannot be overstated. The future of electronic components relies on the ability to adapt and improve, ensuring that resistors like Resistor 4 remain at the forefront of electronic design and application.
VII. References
A comprehensive list of academic papers, industry reports, and other resources used for research would be included here to provide further reading and validation of the information presented in this article.
What are the Manufacturing Processes of the Latest Resistor 4?
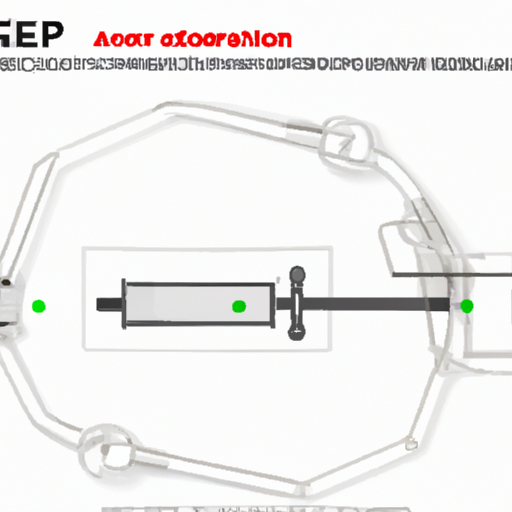
I. Introduction
Resistors are fundamental components in electronic circuits, serving the critical function of controlling current flow. They are essential for protecting sensitive components, dividing voltages, and setting bias points in various applications. Over the years, the evolution of resistors has led to significant advancements in their design and manufacturing processes, culminating in the latest innovation: Resistor 4. This article aims to explore the manufacturing processes behind Resistor 4, highlighting the importance of these processes in enhancing performance and reliability in modern electronics.
II. Understanding Resistor 4
A. Description of Resistor 4 and its Specifications
Resistor 4 represents the latest generation of resistive components, characterized by its high precision, stability, and low temperature coefficient. Typically, Resistor 4 is available in various resistance values, power ratings, and tolerances, making it suitable for a wide range of applications. Its design incorporates advanced materials and manufacturing techniques that contribute to its superior performance compared to earlier resistor models.
B. Applications of Resistor 4 in Modern Electronics
Resistor 4 finds applications across various sectors, including telecommunications, automotive, consumer electronics, and industrial automation. Its high reliability and precision make it ideal for use in critical applications such as signal processing, power management, and sensor interfacing. As electronic devices become more compact and complex, the demand for high-performance resistors like Resistor 4 continues to grow.
C. Importance of Advanced Manufacturing Processes in Enhancing Performance
The performance of Resistor 4 is heavily influenced by the manufacturing processes employed in its production. Advanced techniques ensure that the resistors meet stringent specifications for accuracy, stability, and durability. As technology evolves, the need for innovative manufacturing processes becomes increasingly important to keep pace with the demands of modern electronics.
III. Key Manufacturing Processes
A. Material Selection
1. Types of Materials Used
The choice of materials is crucial in resistor manufacturing. Resistor 4 typically utilizes a variety of materials, including carbon, metal film, and thick film. Each material has unique properties that affect the resistor's performance. For instance, metal film resistors are known for their low noise and high stability, while thick film resistors offer robustness and cost-effectiveness.
2. Importance of Material Properties
Material properties such as temperature coefficient, stability, and resistance tolerance play a significant role in the overall performance of Resistor 4. A low temperature coefficient ensures that the resistor maintains its resistance value across a wide temperature range, which is essential for applications in varying environmental conditions.
B. Design and Engineering
1. Computer-Aided Design (CAD) in Resistor Development
The design phase of Resistor 4 involves the use of computer-aided design (CAD) software to create precise models of the resistor. CAD allows engineers to visualize the resistor's structure and optimize its dimensions for performance. This step is critical in ensuring that the resistor meets the required specifications before moving on to fabrication.
2. Simulation and Modeling for Performance Optimization
Simulation tools are employed to model the electrical behavior of Resistor 4 under different conditions. By simulating various scenarios, engineers can identify potential issues and make necessary adjustments to the design. This iterative process helps in optimizing the resistor's performance and reliability.
C. Fabrication Techniques
1. Thin Film Technology
a. Process Overview
Thin film technology involves depositing a thin layer of resistive material onto a substrate. This process typically uses techniques such as sputtering or chemical vapor deposition (CVD). The thin film is then patterned to create the desired resistance value.
b. Advantages and Applications
Thin film resistors offer high precision and stability, making them suitable for applications in precision instrumentation and high-frequency circuits. Their small size and low parasitic capacitance also make them ideal for compact electronic devices.
2. Thick Film Technology
a. Process Overview
Thick film technology, on the other hand, involves printing a paste of resistive material onto a substrate and then firing it at high temperatures to create a solid layer. This method allows for the production of resistors with higher power ratings and larger physical sizes.
b. Advantages and Applications
Thick film resistors are known for their robustness and cost-effectiveness, making them widely used in consumer electronics and industrial applications. They can handle higher power levels and are less sensitive to environmental factors.
3. Wirewound Resistors
a. Process Overview
Wirewound resistors are made by winding a resistive wire around a core. This method allows for precise control over the resistance value and power rating. The wire is typically made of materials such as nickel-chromium or copper-nickel alloys.
b. Advantages and Applications
Wirewound resistors are known for their high power handling capabilities and excellent stability. They are commonly used in applications requiring high precision and reliability, such as power supplies and audio equipment.
D. Assembly and Packaging
1. Steps in Assembling Resistors
The assembly of Resistor 4 involves several steps, including attaching leads, soldering, and testing. Each step is performed with precision to ensure that the final product meets quality standards.
2. Importance of Packaging in Performance and Reliability
Packaging plays a crucial role in protecting resistors from environmental factors such as moisture, dust, and mechanical stress. The choice of packaging material and design can significantly impact the resistor's performance and longevity.
3. Innovations in Packaging Technology
Recent advancements in packaging technology have led to the development of more compact and efficient designs. Innovations such as surface-mount technology (SMT) allow for easier integration into modern electronic circuits, enhancing the overall performance of Resistor 4.
IV. Quality Control and Testing
A. Importance of Quality Assurance in Resistor Manufacturing
Quality assurance is a critical aspect of resistor manufacturing. Ensuring that each resistor meets the required specifications is essential for maintaining reliability and performance in electronic circuits.
B. Testing Methods for Performance Evaluation
1. Electrical Testing
Electrical testing involves measuring the resistance value, tolerance, and temperature coefficient of the resistor. These tests ensure that the resistor performs as expected under various conditions.
2. Environmental Testing
Environmental testing evaluates the resistor's performance under different environmental conditions, such as temperature extremes and humidity. This testing is crucial for applications where resistors may be exposed to harsh conditions.
C. Standards and Certifications
Manufacturers of Resistor 4 must adhere to various standards and certifications, such as ISO and RoHS. These certifications ensure that the resistors meet international quality and safety standards, providing assurance to customers regarding their reliability.
V. Innovations and Future Trends
A. Emerging Technologies in Resistor Manufacturing
The resistor manufacturing industry is witnessing the emergence of new technologies, such as nanomaterials and advanced ceramics. These materials offer the potential for even higher performance and reliability in resistors.
B. The Role of Automation and Industry 4.0
Automation and Industry 4.0 are transforming the manufacturing landscape, enabling more efficient production processes and improved quality control. Smart manufacturing techniques allow for real-time monitoring and adjustments, enhancing the overall efficiency of resistor production.
C. Future Challenges and Opportunities in Resistor Design and Manufacturing
As electronic devices continue to evolve, resistor manufacturers face challenges such as miniaturization and increased performance demands. However, these challenges also present opportunities for innovation and the development of new resistor technologies that can meet the needs of future applications.
VI. Conclusion
In conclusion, the manufacturing processes of Resistor 4 play a vital role in its performance and reliability in modern electronics. From material selection to advanced fabrication techniques, each step in the manufacturing process contributes to the overall quality of the resistor. As technology continues to advance, the importance of continuous innovation in resistor manufacturing cannot be overstated. The future of electronic components relies on the ability to adapt and improve, ensuring that resistors like Resistor 4 remain at the forefront of electronic design and application.
VII. References
A comprehensive list of academic papers, industry reports, and other resources used for research would be included here to provide further reading and validation of the information presented in this article.